Basics of Batch Tracking
For an enterprise, inventory management is the linchpin of its operations. It directly impacts a company's financial health, customer satisfaction, and overall efficiency. Inventory management helps in optimizing storage space, reducing holding costs, and enabling timely delivery of products to customers. Batch tracking is an integral component of inventory management. It provides a detailed layer of control and traceability within the inventory system. By tracking items in batches, businesses can better manage stock rotation, identify the origin and quality of products, and streamline recall processes if necessary.
What is Batch Tracking?
Batch tracking, also known as lot tracking, is a crucial part of inventory management. It uses batch numbers to group and monitor stocks with similar features, applicable in batch production to trace goods across the supply chain. By assigning numbers that carry diverse data, it enables traceability, ensuring regulatory compliance and optimizing manufacturing and inventory processes.
Why is Batch Tracking Important to Businesses?
Batch tracking is essential for businesses for several key reasons.
First and foremost, it serves as a powerful quality control tool. By tracking products by batch, companies can isolate and inspect items from specific production runs, making it easier to identify and resolve potential issues before they affect the entire inventory. For instance, in industries like food and beverage, batch tracking allows businesses to trace quality issues back to their source, helping protect consumer health and the brand’s reputation.
Secondly, batch tracking plays a critical role in recall management. If a defect or safety concern arises, businesses can quickly identify which specific batches are impacted and act swiftly to notify customers and remove products from circulation, reducing risk and minimizing harm.
Lastly, batch tracking improves supply chain transparency and credibility. By demonstrating a solid batch tracking system, companies signal to suppliers and customers that they prioritize product quality and inventory management. This can lead to stronger business relationships, attract new customers, and provide a competitive advantage in the market.
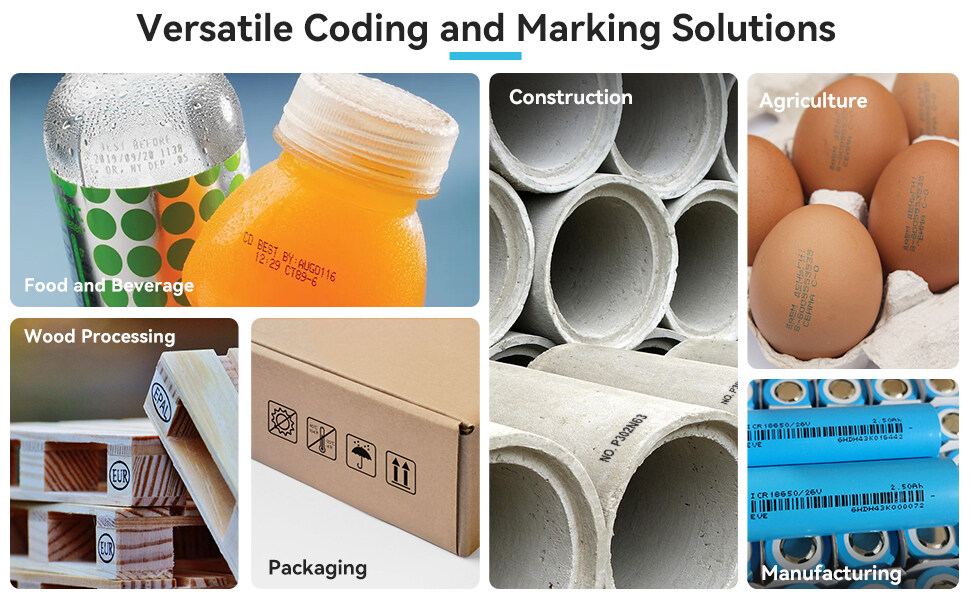
What is the Difference Between Batch Tracking and Lot Tracking?
In inventory management, the terms "batch" and "lot" are often used interchangeably, yet they have nuanced differences. A "batch" specifically refers to a group of products made in a single production run, sharing identical production conditions, date, and time. In contrast, a "lot" has a broader meaning and can denote a batch or any collection of products for tracking purposes. Similarly, batch tracking and lot tracking are related but distinct. A lot code groups products with common production traits and is vital for tracing from production to the end consumer, especially for recalls and defect identification. When we mention a 'lot', it implies a set of products with similar characteristics. A batch code, however, focuses on a specific production run, capturing details like production time, date, and raw materials used. It helps isolate and resolve issues within a particular production run to ensure product quality.
Who Needs to Use Batch Tracking?
A wide range of businesses can benefit from batch tracking. Manufacturers, especially those in regulated industries like food and beverage, pharmaceuticals, and cosmetics, rely on batch tracking to ensure product safety and quality. Distributors also find it useful to manage incoming and outgoing stock, especially when dealing with large volumes of products. Retailers can use batch tracking to manage product recalls more effectively and to ensure that they are selling fresh and high-quality items. In short, any business that wants to have better control over its inventory, improve product quality, and enhance customer satisfaction can benefit from implementing batch tracking.
Benefits of Batch Tracking
The benefits of batch tracking are numerous.
- Improved quality control: By closely monitoring batches, businesses can identify and correct any quality issues early in the production process.
- Simplifies recall process: In the event of a product recall, having batch-specific information readily available allows companies to quickly identify and retrieve the affected products, minimizing the impact on customers and the company's reputation.
- Optimizing inventory management: Provide real-time product status and location data, optimizing stock levels and reducing costs.
- Enhance customer trust: Customers are more likely to purchase products from a company that can demonstrate strict quality control through batch tracking.
- Regulatory compliance: Help businesses meet strict regulations on product traceability and safety, avoiding fines and legal issues.
- Better supply chain: Offer insights into the supply chain, facilitating a more agile response.
How to Implement Batch Tracking?
STEP 1: Set Up Batch Numbers
To create and assign batch numbers effectively, first, clearly define the criteria and format for creating them. Batch numbers are designed to identify products made by the same manufacturer on the same date with the same materials. Ensure your production process records these details accurately. Make sure the batch number format is distinguishable from SKU numbers to avoid confusion. It should be simple yet comprehensive enough to hold all the necessary information for traceability. A common approach is to use a combination of letters and numbers that may include the production date, production line number, or a sequential identifier. For example, to create and assign a batch number like "230915-A-001", "230915" represents the production date (September 15, 2023), "A" represents the production line, and "001" is the sequential number for that day's production on that line.
STEP 2: Record Batch Information
For every batch of products, creating a detailed tracking record is essential as it significantly facilitates batch tracking. This record should include details like:
- Batch number
- Date of production
- List of ingredients or materials used
- Production location
- Personnel involved
- Quality control checks
Make sure this information is accurate and consistently recorded.
STEP 3: Select a Printing Device
To physically mark the batches, you need to select an appropriate printing device. Large industrial printers and handheld printers are two main contenders, each with their own set of characteristics.
Large industrial printers are great for high-volume production. They print fast and precisely, integrating well with automated lines. However, they're expensive, take up a lot of space, and are hard to move.
Handheld printers are an excellent choice due to their portability and flexibility. They can print batch numbers directly on products or packaging anywhere in the facility. Compared with the large industrial printers, they're affordable and easy to use. But they're not as fast as industrial printers, have limited daily output, and may struggle with complex prints. When picking one, think about print quality, durability, battery life, and material compatibility.
Businesses should weigh production volume, budget, and functionality to pick the right printer.
STEP 4: Batch Number Printing and Coding
Using the selected printing device, print the batch numbers and any other relevant batch-related information (such as expiration dates, lot sizes) onto the products or their packaging. It's important that the batch coding results in clear and legible markings.
STEP 5: Use a Tracking System and Start Batch Tracking
Use a tracking system that empowers you to document the movement and status of every batch as it advances through your business operations. This can be a combination of software, hardware, and manual record-keeping. The tracking system should be able to record the location of each batch at every stage, from production to distribution and eventually to the customer. By regularly updating the system, businesses can have real-time visibility into their batch inventory and ensure efficient batch tracking.
In Conclusion
Batch tracking is important for businesses across various industries, especially for those aiming to maintain high-quality standards, comply with regulations, and optimize their inventory management. By understanding the basics of batch tracking and following the steps to implement it, businesses can cut down on costs associated with waste, overstocking, or product recalls. Moreover, it directly contributes to enhanced customer satisfaction, as customers are more likely to trust businesses that can precisely manage product quality. In summary, businesses should consider implementing batch tracking as part of their inventory management system, whether it is a manual or software-based system.
Ask Question
No questions and answers