Top Printers for Printing on Plastic Materials: Comprehensive Guide
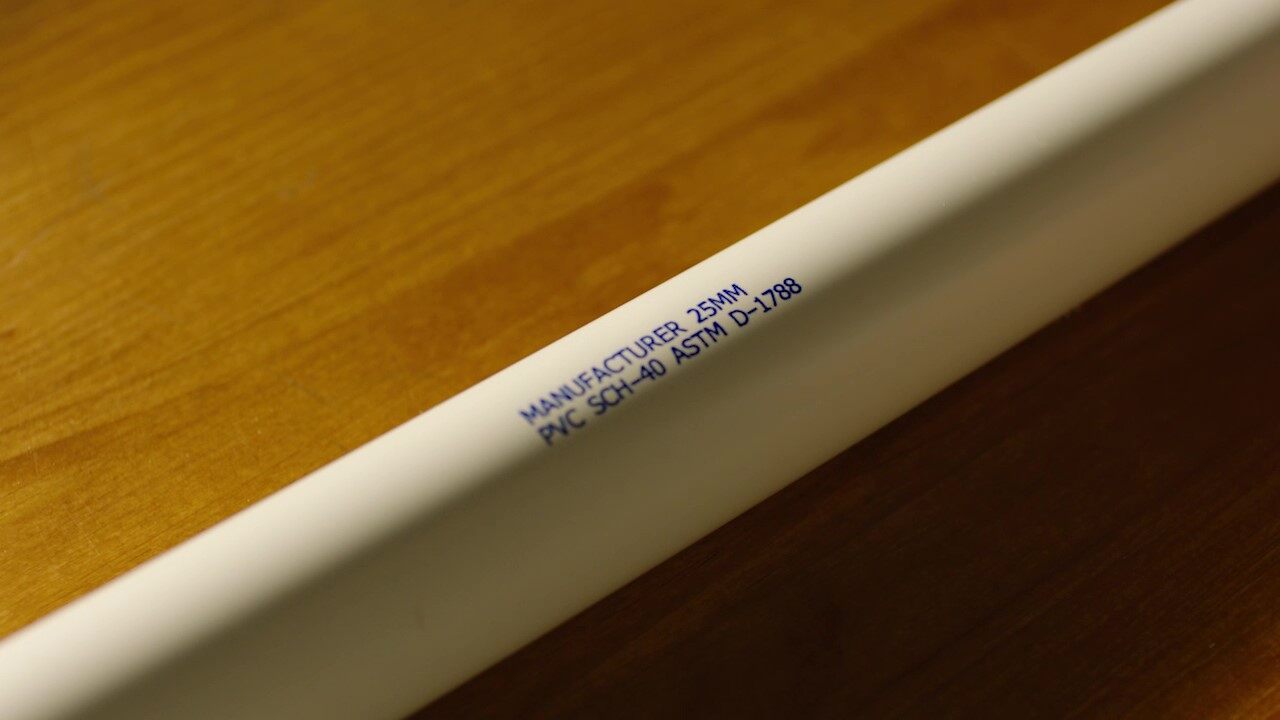
Plastic is everywhere, from food packaging to medical equipment. So, it's no surprise that the ability to print on plastic materials is incredibly important. When it comes to printing on plastic materials, choosing the right printer is crucial for achieving quality results. Whether for industrial labeling, creative projects, or custom packaging, the type of printer you use can make all the difference. In this article, we will first introduce common plastics used in various applications, followed by an exploration of printer types.
Types of Plastic Materials
Before we delve into the printers that can print directly onto plastic materials, let go through different types of plastics that can be used for printing.
1. Polyethylene Terephthalate (PET):
Commonly used for beverage bottles and food packaging, PET is known for its strength and flexibility.
2. High-Density Polyethylene (HDPE):
HDPE is found in items like plastic bottles and toys, valued for its durability and chemical resistance.
3. Polyvinyl Chloride (PVC):
Used in construction for pipes and home products, PVC is versatile and robust.
4. Polycarbonate (PC):
Known for its transparency and high-temperature resistance, PC is used in applications requiring visual clarity and strength.
5. Polypropylene (PP):
Frequently used in packaging, automotive parts, and textiles, PP is noted for its fatigue resistance.
What Type of Printer Is Suitable for Printing on Plastic Materials?
1. Digital InkJet Printing:
- Process: Digital InkJet printing uses inkjet technology to print high-quality images on plastic. It involves preparing a digital file, printing the image with inkjet nozzles, and drying the ink for a smudge-proof, water-resistant finish.
- Applications: Ideal for personalized items like gift cards, ID cards, and loyalty cards.
- Advantages: Quick turnaround times, lower costs, and customizable for small batches.
2. Screen Printing:
- Process: Screen printing transfers ink through a stencil onto plastic substrates. It involves preparing artwork, creating a stencil, preparing specialized ink, and printing the image.
- Applications: Used for substrates where durable and long-lasting prints are required.
- Advantages: Cost-efficient for large quantities and provides durable prints.
3. Flexo Printing:
- Process: Flexo printing uses flexible photopolymer printing plates. It involves prepress preparation, ink preparation, and a multi-station printing process.
- Applications: Suitable for labels, packaging, bags, and more.
- Advantages: High-quality images at high speeds, versatile for various plastic substrates.
4. UV Litho Printing:
- Process: UV Lithography uses UV light to cure ink. It includes designing artwork, preparing printing plates, and using UV ink for printing.
- Applications: Common in cosmetic, pharmaceutical, and food industries for packaging and labels.
- Advantages: Produces high-quality images with fine details and vibrant colors, with fast drying time.
5. Pad Printing:
- Process: Pad printing transfers images from a laser-engraved plate to a 3D object using a silicone pad. It involves plate etching, ink preparation, and ink transfer.
- Applications: Effective for curved or irregular surfaces.
- Advantages: Capable of printing fine details and intricate designs.
6. Laser Printing:
- Process: Laser printing uses a focused laser beam to heat and melt the plastic surface, creating designs or images.
- Applications: Suitable for high-quality, precise, and detailed prints.
- Advantages: Non-contact process reducing material damage risk, environmentally friendly with minimal waste.
7. Handheld Thermal Inkjet Printing (TIJ)
- Process: Handheld Thermal Inkjet printers are portable handheld printers that use heat to expel ink droplets onto the plastic surface. This method is known for its portability and the ability to produce high-resolution prints.
- Applications: Ideal for detailed, small-scale printing on plastic substrates on the go, including packaging and labeling.
- Advantages: Portable and easy use, high-resolution printing, relatively low maintenance. Particularly useful for businesses requiring detailed printing with a compact setup.
Each of these printing technologies is suited for specific types of plastic materials and applications, from packaging and labeling to creating decorative and functional elements on plastic products. The choice of printer depends on factors such as the type of plastic, the required print quality, production volume, and the specific application.
Where to Find a Reliable Handheld Printer for Printing on Plastics?
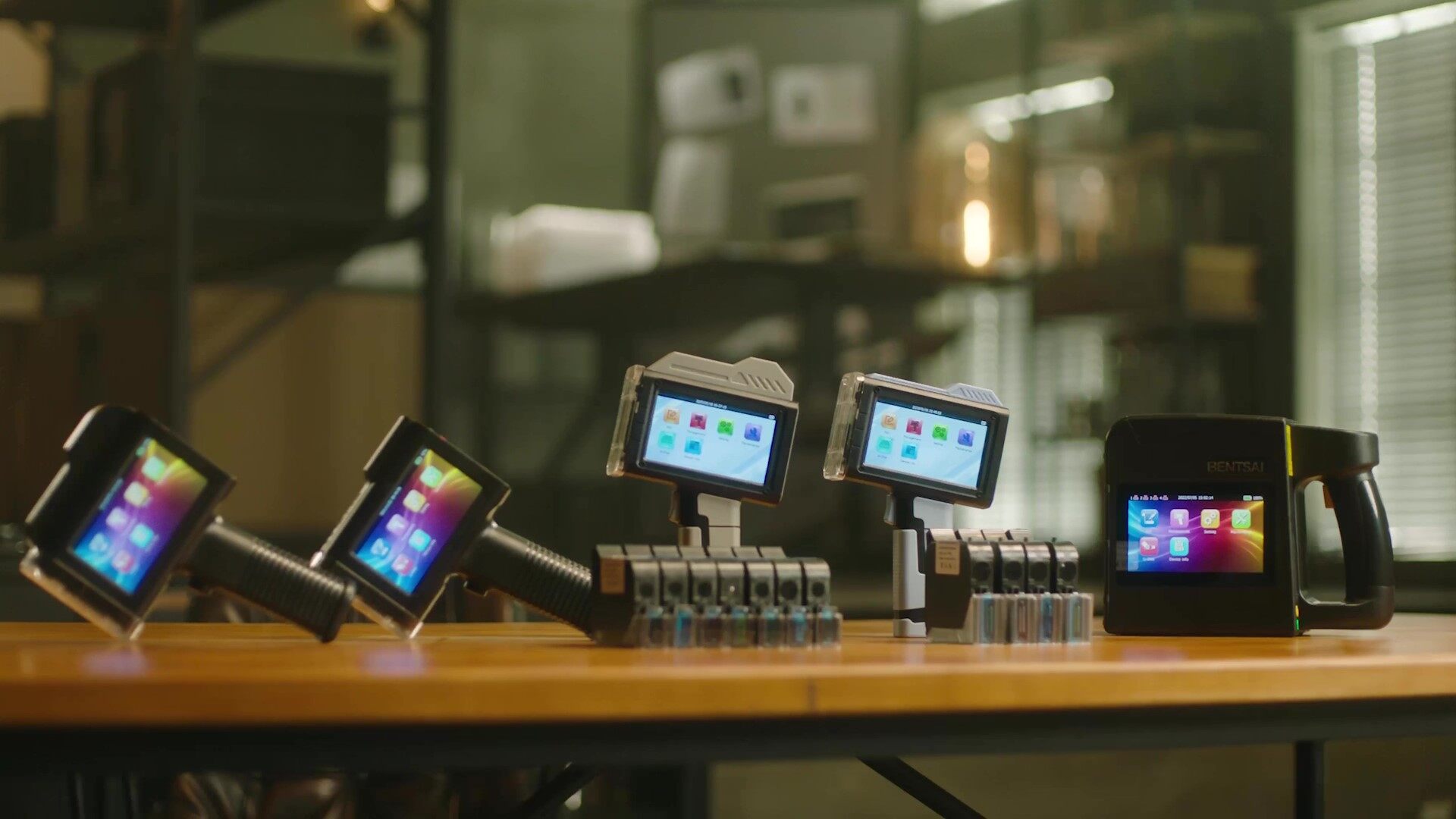
If you run a business that requires efficiently labeling products, like dating PVC bottles, marking serial numbers on plastic pieces, or stamping other essential information directly onto plastic surfaces, a handheld printer offers a cost-effective and versatile solution.
When searching for a reliable handheld printer for these tasks, it's crucial to choose a manufacturer known for quality and innovation. In this regard, Bentsai stands out, offering a range of handheld inkjet printers that can print from 2.5mm to 100mm optional. These are specifically designed for ease of use, efficiency, and high-quality printing on plastic surfaces. Ideal for businesses that need flexible, precise, and durable printing solutions, Bentsai's printers cater to both small-scale and industrial printing requirements, ensuring that your business's labeling needs are met with professionalism and ease.
Summary
Choosing the right printer for plastic materials depends on your specific needs, including the scale of your operations, the type of plastic you are printing on, and the desired print quality. Whether it's a handheld inkjet printer for on-the-go printing or an industrial machine for high-volume production, there is a printing solution to meet every requirement. For more details on specialized handheld inkjet printers, consider exploring the offerings from brands like Bentsai, known for their expertise in this area.
Ask Question
No questions and answers